Uneven whiteness
Uneven white is very common problem in the knitted fabric , either it is processed in Soft flow or in CBR. with some precaution it can be permanently cured .
In knitted cotton fabric, as we know it is in general processed in soft flow dyeing machine , Which is running in rope form. Hence chances of unevenness is always present. For this we need to insure that
1- fabric is running properly .
2- Temperature profile of the Process.
3- Chemical concentration is as per requirement.
4- Residual of the Peroxide is not in the fabric after end of the process.
5- Oba selection is correct .
6- Application of OBA is done at correct pH.
Knitted Fabric Runnability
Runnability of the knitted fabric in the soft flow depends on the rope length of the fabric . Hence it is very important that before loading the fabric we need to calculate the rope length of each tube. it should almost same with the tolerance of +/- 10 mtrs .
The loading capacity is the next thing need to be check. Loading capacity means the maximum height of the fabric in the chamber without falling here and there . This need to fix by seeing the chamber condition. As it depends on the type of plaiting arrangement inside the chamber. If plaiting is uneven then height of the plaited fabric will be uneven, and we will face lot of fabric entanglement .
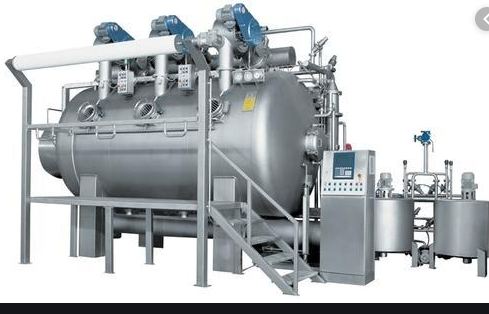
Temperature profile of the Process.
In the cotton bleaching the temperature profile is very important. The addition of chemical and temperature rising should not ever together . It is based on simple physical chemistry formula. PV=nRT. So if we are adding any chemical , volume is increasing, and if increase the temperature at same time, then pressure will also increase . this will result in all factor increment together , which P, V, T. it will give uneven reaction with cotton. This unevenness can not ever corrected at later stage by any means. As here cellulose is getting uneven bleached.
Chemical concentration is as per requirement.
In general we are using caustic and peroxide to do bleaching of the fabric . We need to insure h2o2 is not getting decompose very fast . and it is not left too much un reacted also at the end of the process.
Excess H2O2 , need to neutralise in the further washes . If H2O2 remains in the fabric after unloading in the fabric then it may give yellowing effect in the finished fabric.
If pH of the fabric at the end of the process should be 5 to 6.5 in core level.
Too acidic will also give yellowing of fabric . And little alkailne or towards neutral will give failure of phenolic yellowing . It means fabric may turned yellowing in the polythene packing condition due to storage
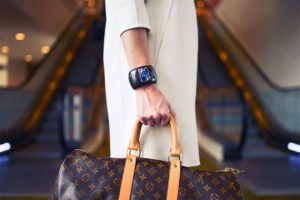
Residual Peroxide in Fabric
Residual of H2O2 should not be left out in the fabric after completion of process. It is very hard to calculate the exact amount of H2O2 needed . In general 0.5 to 0.8 % peroxide remain in the bath after completion of process.
So if we add 0.75 gpl to 1 gpl Sodium Hydro sulphite in the next hot wash , It will kill peroxide , And will improve the brightness of white . Other than this there is one more advantage of this step that some colour contamination fibre will also get reduce , and we can reduce the colour fibre level in the finished fabric also.