Definition
and scope of technical textiles
The definition of technical textiles adopted by the authoritative Textile Terms and Definitions, published by the Textile Institute, is ‘textile materials and products manufactured primarily for their technical and performance properties rather than their aesthetic or decorative characteristics’
Such a brief description clearly leaves considerable scope for interpretation, especially when an increasing number of textile products are combining both per- formance and decorative properties and functions in equal measure. Examples are flame retardant furnishings and ‘breathable’ leisurewear. Indeed, no two published sources, industry bodies or statistical organisations ever seem to adopt precisely the same approach when it comes to describing and categorising specific products and applications as technical textiles.
It is perhaps not surprising that any attempt to define too closely and too rigidly the scope and content of technical textiles and their markets is doomed to failure. In what is one of the most dynamic and broad ranging areas of modern textiles, materials, processes, products and applications are all changing too rapidly to define and document. There are even important linguistic and cultural perceptions of what constitutes a technical textile from geographical region to region in what is now a global industry and marketplace.
1.1 -Technical or industrial textiles: what’s in a name?
For many years, the term ‘industrial textiles’ was widely used to encompass all textile products other than those intended for apparel, household and furnishing end-uses. It is a description still more widely favoured in the USA than in Europe and elsewhere .
This usage has seemed increasingly inappropriate in the face of developing applications of textiles for medical, hygiene, sporting, transportation, construction, agricultural and many other clearly non-industrial purposes. Industrial textiles are now more often viewed as a subgroup of a wider category of technical textiles, referring specifically to those textile products used in the course of manufacturing operations (such as filters, machine clothing, conveyor belts, abrasive substrates etc.) or which are incorporated into other industrial products (such as electrical components and cables, flexible seals and diaphragms, or acoustic and thermal insulation for domes- tic and industrial appliances).
If this revised definition of industrial textiles is still far from satisfactory, then the problems of finding a coherent and universally acceptable description and classifi- cation of the scope of technical textiles are even greater. Several schemes have been proposed. For example, the leading international trade exhibition for technical textiles, Techtextil (organised biennially since the late 1980s by Messe Frankfurt in Germany and also in Osaka, Japan), defines 12 main application areas (of which textiles for industrial applications represent only one group):
- agrotech: agriculture, aquaculture, horticulture and forestry
- buildtech: building and construction
- clothtech: technical components of footwear and clothing
- geotech: geotextiles and civil engineering
- hometech: technical components of furniture, household textiles and floorcoverings
- indutech: filtration, conveying, cleaning and other industrial uses
- medtech: hygiene and medical
- mobiltech: automobiles, shipping, railways and aerospace
- oekotech: environmental protection
- packtech: packaging
- protech: personal and property protection
- sportech: sport and
The search for an all embracing term to describe these textiles is not confined to the words ‘technical’ and ‘industrial’. Terms such as performance textiles, functional textiles, engineered textiles and high-tech textiles are also all used in various contexts, sometimes with a relatively specific meaning (performance textiles are frequently used to describe the fabrics used in activity clothing), but more often with little or no precise significance.
If the adjective ‘technical’ is difficult to define with any precision, then so too is the scope of the term textiles. Figure 1.1 summarises the principal materials, processes and products which are commonly regarded as falling within the scope of technical textiles manufacturing.
However, there remain many grey areas. For example, the manufacture and pro- cessing of metallic wires into products such as cables, woven or knitted screens and meshes, and reinforcing carcasses for tyres are not generally regarded as lying within the scope of the textile industry. This is despite the fact that many of the techniques employed and the final products obtained are closely related to conventional textile fibre equivalents.
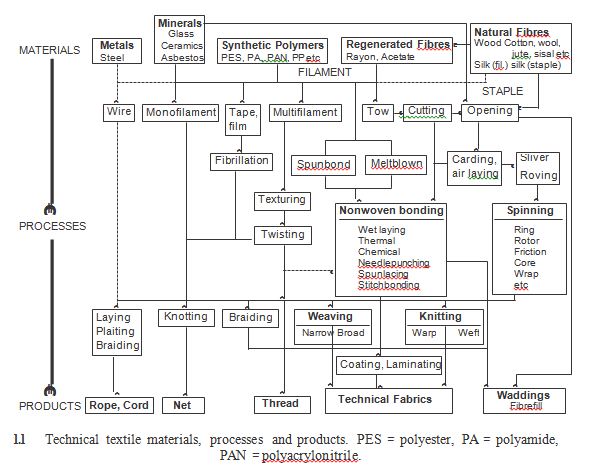
Within the composites industry, woven, knitted, braided, nonwoven and wound yarn reinforcements made from glass, carbon fibre and organic polymer materials such as aramids are all now widely accepted as being technical textile products. On the other hand, more loosely structured reinforcing materials such as chopped strand mat, milled glass and pulped organic fibres are often excluded.
The nonwovens industry has developed from several different technology directions, including paper manufacturing. The current definition of a nonwoven promulgated, for example, under the International Standards Organization standard ISO 90923 acknowledges a number of borderline areas, including wet-laid products and extruded meshes and nets. Likewise, distinctions between textile fibres and fil- aments, slit or fibrillated films, monofilaments and extruded plastics inevitably boil down to some fairly arbitrary and artificial criteria. Diameter or width is often used as the defining characteristic, irrespective of the technologies used or the end-uses served. Many of the definitions and categories embodied within existing industry statistics reflect historical divisions of the main manufacturing sectors rather than a functional or market-based view of the products involved.
Polymer membranes, composite materials and extruded grids and nets are other products which challenge traditional notions of the scope of technical textile ma- terials, processes and products. Increasingly, technical textiles are likely to find their place within a broader industry and market for ‘flexible engineering materials’ (Fig. 1.2). A number of companies and groups have already adopted this outlook and operate across the boundaries of traditional industry sectors, focusing a range of materials, process technologies and product capabilities upon specific functions and markets such as filtration and health care.
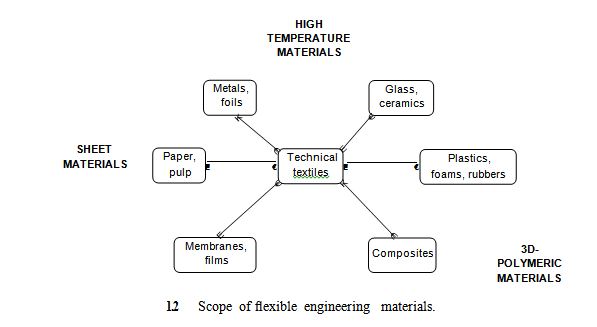
1.3 Inconsistent statistical reporting
To add to this complexity, different geographical regions and countries tend to adopt rather different viewpoints and definitions with regard to all of the above. A widely quoted misconception that technical textiles in Japan account for over 40% of all textile output or nearly twice the level in Western Europe can largely be put down to the different statistical bases employed. In Europe, the most authoritative source of fibre consumption (and therefore textile output) data is CIRFS (Comité International de la Rayonne et des Fibres Synthétiques), the European artificial fibre producers association. However, CIRFS’ reported statistics (at least until recently) have specifically excluded tape and film yarns (a significant proportion of all polyolefin textiles), coarser monofilaments and all glass products (as well as natural fibres such as jute, flax, sisal, etc.). The merger of CIRFS and EATP, the European Polyolefin Textiles Association, should go some way towards resolving this anomaly.
The Japanese ‘Chemical’ Fibres Manufacturers Association, JCFA, at the other extreme, includes all these products, including natural fibres, within its definition of technical/industrial textiles while the Fiber Statistics Bureau in the USA includes polyolefin tape and monofilament yarns but excludes glass. Table 1.1 attempts to restate the relative usage of the main technical fibres and yarns on a more consis- tent basis.
In this new light, Japan still retains a leading position worldwide in terms of the proportion of its total textile manufacturing output devoted to technical textiles. However, this is largely a reflection of the importance of its automotive manufacturing industry (a key user of technical textiles) combined with the rela- tively smaller size of its apparel and furnishing textile sectors (especially floor coverings). The USA apparently accounts for the lowest proportion of technical textile output of the three major industrial regions but still produces and consumes the largest quantity per capita, especially when all glass textile and technical fibre uses are included
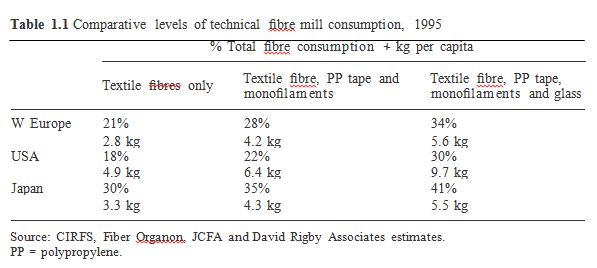
List of contributors
Professor S C Anand
Faculty of Technology, Bolton Institute, Deane Road, Bolton BL3 5AB, UK
Professor P Bajaj
Department of Textile Technology, Indian Institute of Technology, Hauz Khas, New Delhi, India
Mr C Byrne
David Rigby Associates, Peter House, St Peter’s Square, Manchester M1 5AQ, UK
Dr X Chen
Department of Textiles, UMIST, P O Box 88, Sackville Street, Manchester M60 1QD, UK
Mr W Fung
Collins and Aikman, P O Box 29, Warley Mills, Walkden, Manchester M28 3WG, UK
Dr R H Gong
Department of Textiles, UMIST, P O Box 88, Sackville Street, Manchester M60 1QD, UK
Dr M Hall
Department of Textiles, Faculty of Technology, Bolton Institute, Deane Road, Bolton BL3 5AB, UK
Mr E Hardman
Madison Filters (formerly Scapa Filtration), Haslingden, Rossendale, Lancashire, UK
xvi List of contributors
Dr I Holme
Department of Textiles, University of Leeds, Leeds LS2 1JT, UK
Dr D Holmes
Department of Textiles, Faculty of Technology, Bolton Institute, Deane Road, Bolton BL3 5AB, UK
Dr M Miraftab
Department of Textiles, Faculty of Technology, Bolton Institute, Deane Road, Bolton BL3 5AB, UK
Dr S Ogin
School of Mechanical and Materials Engineering, University of Surrey, Guildford, Surrey GU2 7HX, UK
Dr M Pritchard
Department of the Built Environment, Faculty of Technology, Bolton Institute, Deane Road, Bolton BL3 5AB, UK
Professor P R Rankilor
9 Blairgowrie Drive, West Tytherington, Macclesfield, Cheshire SK10 2UJ, UK
Mr A J Rigby
Department of Textiles, Faculty of Technology, Bolton Institute, Deane Road, Bolton BL3 5AB, UK
Professor S W Sarsby
Department of the Built Environment, Faculty of Technology, Bolton Institute, Deane Road, Bolton BL3 5AB, UK
Dr R A Scott
MOD, Defence Clothing and Textiles Agency Science and Technology Division, Flagstaff Road, Colchester, Essex CO2 7SS, UK
Professor K Slater
Department of Textiles, University of Guelph, Guelph, Ontario N1G 2W1, Canada
Dr P Smith
26 Newhall Park, Otley, Leeds LS21 2RD, UK
Mr W Sondhelm
10 Bowlacre Road, Hyde, Cheshire SK14 5ES, UK